Preventative maintenance refers to tasks that maintain assets on a regular basis to optimize performance and prevent unexpected breakdowns that could push up asset tracking costs.
Depending on the type of asset, preventative maintenance can include many different schedules or types of software. Assets might receive maintenance check-ins based on hours used or time since the previous checkup. Machine learning software might even generate custom schedules for the most optimized preventative maintenance.
Done right, a preventative maintenance system maximizes asset lifecycles, fixing your equipment before it breaks in order to keep the entire operation running smoothly.
In this guide:
Why Is Preventative Maintenance Important?
Preventative maintenance is core to any business that uses physical or non-physical assets for one big reason: It’s the only way to produce the absolute best return on the investment in those assets.
Preventative maintenance saves money in four ways. It maximally extends the life of each asset, it reduces time and money spent on maintenance, it reduces asset downtime due to breakdowns, and it streamlines any activity dependent on those assets.
Without an asset monitoring plan that puts preventative maintenance front and center, your operation will be stuck with reactive maintenance – the term for a system that fixes an asset only after it’s too late to do anything else.
Instead, the best asset management systems focuses largely on both preventative maintenance and, since asset breakdowns can’t be entirely prevented, saves some room for corrective maintenance, which addresses faulty assets or systems as efficiently as possible.
How Does Preventative Maintenance Work?
A preventative maintenance program starts with an assessment of asset needs, which informs the maintenance tasks required to keep that asset in top condition. Finally, a maintenance schedule is created to optimize the program’s activities. Here are the questions to ask during the general process:
- Assessment: What type of maintenance does each of your assets need? What monetary value is lost when assets are not maintained, and how quickly is it lost? How long is the lifecycle of a perfectly maintained asset?
- Task list creation: What spare parts are required? How many work hours will maintenance take? What total monetary value will go into completing a required task?
- Scheduling: What determines how often each task should be completed for each asset – time, usage, or a custom software? Can tasks be grouped for efficiency? Which team members will complete the tasks?
- Asset retirement: What determines when assets will be replaced – after a set time or a set amount of use? What does this process look like, and who controls it?
Ideally, a preventative maintenance program will operate by itself once it has been planned out and set in motion.
Read our guide to asset lifecycle management for more information.
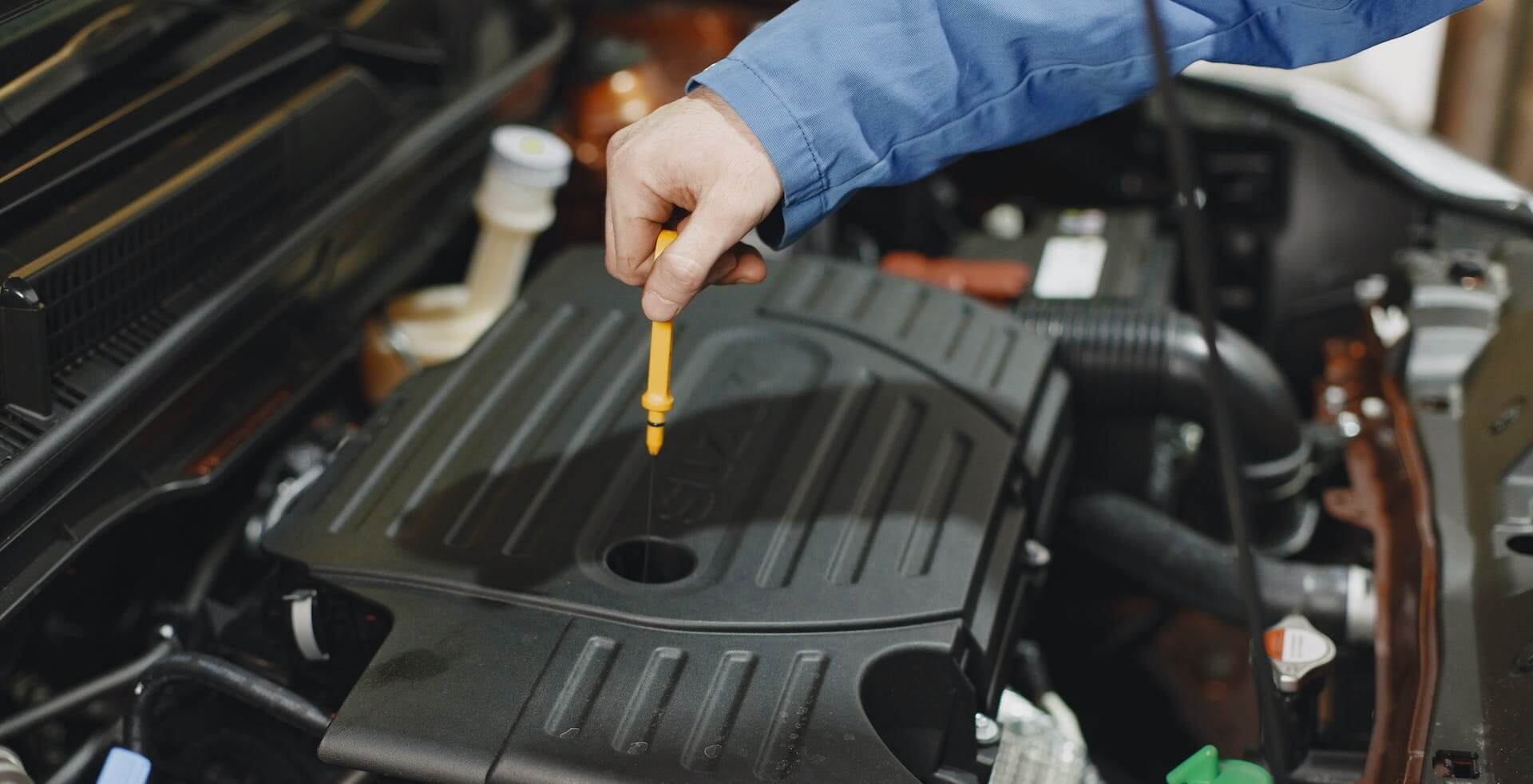
Checking the oil levels in an engine is among the most common types of preventative maintenance.
Examples of preventive maintenance
Preventive maintenance is a general term that covers many different use cases. It includes minor physical tasks like cleaning surfaces, lubricating joints, checking and replacing batteries or oil, or gauging tire pressure and tread depth. It includes more in-depth physical tasks like repairing or replacing major machine parts. It also covers systemic upkeep like testing smoke or carbon dioxide detectors, running fire drills, and verifying electrical systems are up to code.
Types of Preventative Maintenance
You’ll want to complete preventative maintenance during the Goldilocks zone: Not so often that you waste time and resources on maintenance, but not so little that the assets become worse for wear. In practice, this means that preventative maintenance can be completed on a range of different schedules.
Any of the types of schedules below might be useful, or you might try multiple schedules for separate groups of assets within your operation.
Usage-based (UBM)
With usage-based maintenance, assets are due for preventative maintenance based on how much time they have been used since the last checkup.
A usage-based maintenance schedule is common, particularly for vehicles. Since a delivery van might make a delivery nearby or far away, tracking the mileage is a more reliable indicator of maintenance needs than tracking the number of deliveries. You’ll likely need to invest in an asset monitoring system in order to accurately track usage.
Calendar/time-based (TBM)
With time-based maintenance, assets receive preventative maintenance based on the length of time since their previous checkup, regardless of how little or much they have been used. It’s a great approach for assets that are continuously functioning (like air filters) or that must be ready to use at all times (like fire extinguishers).
Predictive maintenance (PdM)
A predictive maintenance schedule uses data analysis to project the optimal time to conduct preventative maintenance on any given asset. This data might include previous breakdowns, work schedules, and maintenance routines. It requires software, and is a good schedule to use for assets that can’t be maintained through an entirely time-based or usage-based schedule.
Prescriptive maintenance (RxM)
Prescriptive maintenance refers to the practice of using machine learning to analyze the state of a group of assets in order to determine their maintenance needs. It’s a more proactive version of predictive maintenance, since it aims to create customized directions.
Benefits of Preventive Maintenance
A well-planned preventive maintenance program comes with a host of benefits, all of which contribute to keeping a business healthy.
- Cost savings – The right preventive maintenance plan balances the longest possible asset life against the fewest maintenance resources. This will ultimately save the most money possible.
- Reduced unplanned downtime – Preventing asset breakdowns will keep them operating as often as needed. If repairs are needed, they will be caught early and fixed as a regular part of the maintenance team’s typical schedule.
- Higher productivity – Business productivity won’t be impacted by asset breakdowns or unexpected repairs. As a result, the business will continue earning the highest revenues possible.
- Better safety, security, and compliance – Assets can be trusted to operate as intended, since they’ll be tested and checked. The alternative is to allow assets to continue operating until failure, which is a recipe for workplace accidents and regulatory violations.
- Increased mechanical skill – Workers will regularly complete many key tasks while maintaining assets. This gives your team a deep practical knowledge of their industry’s machinery or systems over time.
Implementing a Preventative Maintenance Schedule
Your own maintenance schedule hinges on your assets and their service needs. Start by asking yourself all the questions we list in our “How Does Preventative Maintenance Work?” section above.
Then, compile a schedule of all the maintenance tasks your team must complete and what process will tell them when to complete them. The format might be an Excel spreadsheet or, for complex operations, one of the best asset tracking software options available. If your business is already in operation, you can use previous asset usage patterns to inform your schedule. If you are just starting out, manufacturer recommendations or industry experts can be your guides.
You’ll also need to consider two additional practical concerns: Training your maintenance team in the correct procedures, and continually monitoring the entire process to ensure the schedule is actually being met. Asset tracking tags like RFID or barcodes can prove beneficial for logging asset locations, statuses, and conditions.
Preparation can only take you so far. As with most plans, the only way to be sure that you have everything figured out is to start the entire process in motion and adjust it out as you go along. However, with enough effort, you should have a relatively smooth maintenance process, with backup plans ready to implement should something go wrong.
Next Steps
Launching any business maintenance plan starts with preventative maintenance. You’ll need to anticipate all your asset upkeep needs, plan schedules that keep asset lifecycles long and breakdowns minimal, and be
Don’t forget corrective maintenance, either: Even the best prevention can’t solve all your problems, so you’ll need a plan in place for any unexpected asset or system failures that might slip through.
Once you’ve mapped out your entire asset management plan, bring your team into the loop with the right training and resources. Finally, never forget that you can always adjust and tweak your plans as you learn more about how best to keep your assets running.