At an Amazon warehouse in Louisiana, Robin lifts and sorts packages. Hercules moves pods full of goods. Sequoia retrieves items to pick and pack for online orders.
These aren’t the names of Amazon employees – they’re the names of robots Amazon is using at its warehouses to aid human workers and make e-commerce fulfillment operations more efficient. Amazon has deployed more than 750,000 robots across its operations since it acquired Kiva Systems in 2012.
Amazon and other big players, however, are somewhat unique. The majority of warehouses still haven’t automated, according to Christina Dube, director of marketing for the Americas for material handlings company Kardex.
But that could soon change, as the logistics and fulfillment sector intends to spend more than 30% of its capital expenditures on automation. Dube said automation adoption is “skyrocketing” as companies realize they’re challenged by labor and space constraints, and automation could help ease those pain points while offering numerous other benefits and a quick ROI.
For businesses that want to grow, automation is “not optional anymore,” Dube said. “People are jumping in with both feet.”
Get the latest insight in logistics with our free 25 page report:
Key Takeaways
- Warehouse automation is crucial for businesses looking to overcome labor and space constraints and remain competitive.
- Despite industry growth, warehousing employment has remained static at around 1.8 million since late 2021, and automation could be a solution.
- Automation directly improves accuracy, as a single picking error can cost a business around $100.
- A strong Warehouse Management System (WMS) is a necessary foundation before implementing automation solutions.
- The return on investment for automation can be rapid, with over 78% of customers of one provider seeing a return within the first year.
Warehouse Automation Starts With Data
Myriad types of automation and materials handling equipment exist in a warehouse. There are vertical lifts, carousels and conveyor systems.
Across its network, DHL Supply Chain has installed robots that pick goods, unload pallets and wrap items, along with automation such as storage and retrieval systems, sortation technology, autonomous forklifts and much more, according to Omer Rashid, VP of operations development at the company.
But before warehouse operators, 3PLs and shippers get caught up in the shiny objects, they have to focus on the software that connects and coordinates it all, said Ryan Chesterfield, founder of Auto-FC, a consulting firm specializing in warehouse automation.
“If you don’t have a solid warehouse management system … then it’s too early for robotics or conveyor belts,” Chesterfield said.
Warehouse management systems, known as WMS, often connect to other tech related to inventory or transportation coming in and out of the warehouse, such as order management systems (OMS) or transportation management systems (TMS).
DHL has an automation platform that lets it integrate technologies without needing to customize them. At Amazon, cloud infrastructure supported by Amazon Web Services processes data from machines, sensors and cameras – all of which allows the robots to operate effectively.
“Before you bring in expensive equipment, make sure the foundation (your software and your data) is solid.” – Ryan Chesterfield, founder of Auto-FC
“Automation needs structure and data to run,” Chesterfield said. Without that, “the hardware simply won’t work the way you expect it to.”
Five Benefits of Warehouse Automation
Here are just a few reasons to streamline your warehouse’s operations with automated robots.
1. Improved labor conditions
Over the last three years, employment in the warehousing and storage industry has flatlined. As of May, U.S. employment numbers are hovering around 1.8 million, approximately the same they’ve been since November 2021, according to the Bureau of Labor Statistics.
“The new up-and-coming labor force, they don’t want to walk five miles a day through a dingy warehouse that’s lowly lit, picking stuff off shelving. That’s not what they’re looking to do with their life,” Christina Dube, director of marketing for the Americas for material handlings company Kardex
Automation can aid warehouse employees in ways that make the job less physically taxing and more desirable. Unloading boxes involves a lot of bending, lifting and twisting for humans, which can prove strenuous over the course of many hours. At times, warehouse workers have to unload in hot or cold conditions, depending on the weather and the type of trailer.
DHL uses a “Stretch” robot from Boston Dynamics, which automates container unloading. The Stretch bot can unload 700 cases every hour.
The average warehouse worker walks five miles each day, and automation that brings goods to the person can cut down that figure. DHL has deployed robots from Locus Robotics which go up and down the warehouse aisles, finding items and transporting them to warehouse associates to pick.
“Our associates spend less time walking long distances and pushing heavy carts and focus more on value-added work,” Omer Rashid, VP of operations development at DHL Supply Chains
DHL discovered that automation and robotics were “great recruiting tools. We’ve found that associates want to work in high tech environments,” Rashid said.
The flip side to automation creating a more efficient labor environment is that it could lead to some job displacement. A study from the U.S. Government Accountability Office found that workers who perform routine tasks see the greatest disruptions from automation, and more robots in manufacturing and warehousing could alter the kinds of skills needed for current and future jobs.
But Dube said it’s not about replacing labor but rather providing more skilled jobs in hopes of reducing turnover and building a more resilient labor force.
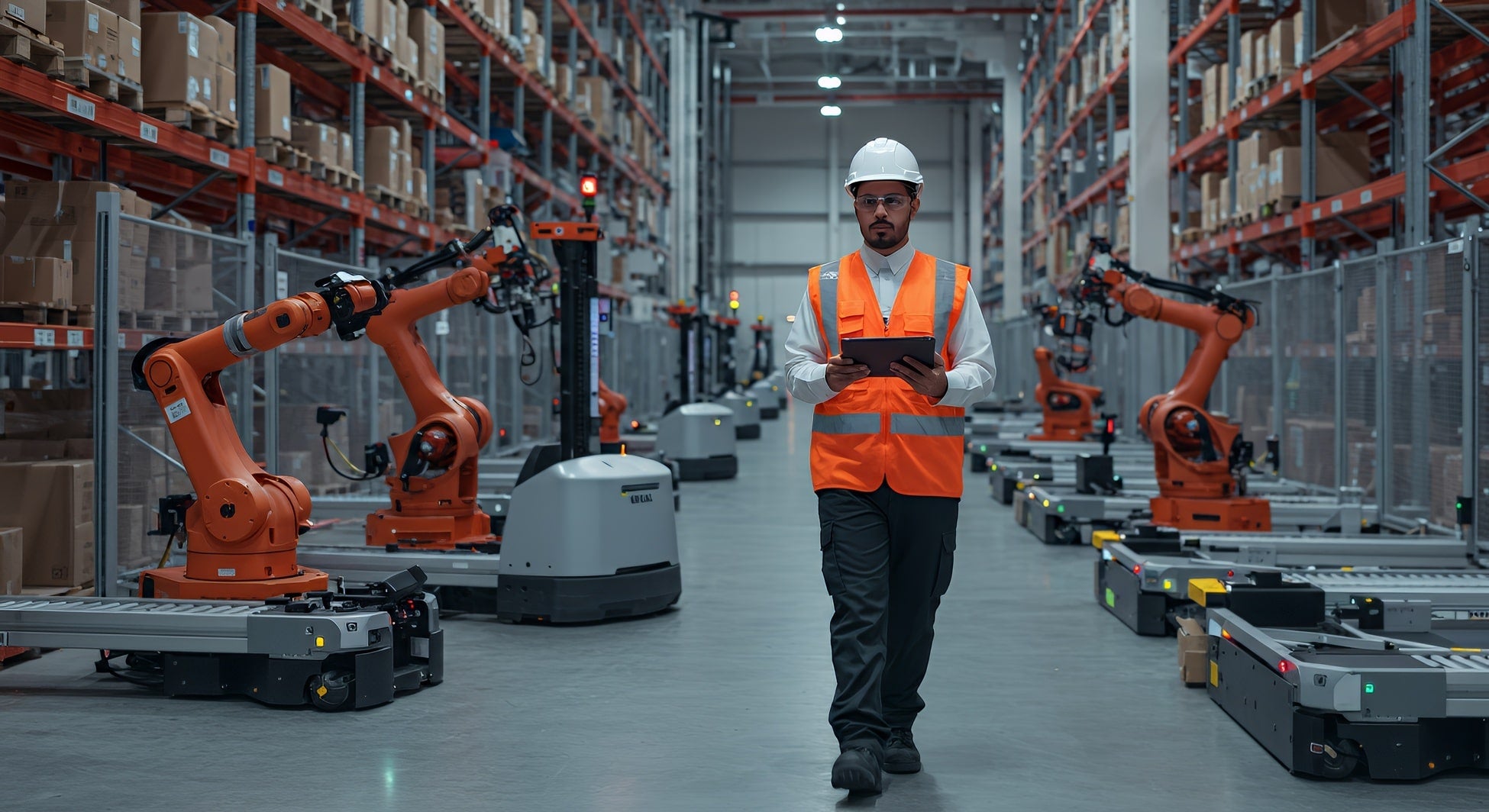
2. Better use of space
Warehouses tend to be tall, with ceilings around 30 to 40 feet. But most vertical storage racks and shelves, especially if warehouses want to store goods within reasonable reach for employees, are eight to 12 feet tall.
“It’s a lot of wasted space,” Dube said.
Automated solutions can transport goods up and down so that vertical space is maximized and workers don’t need to bend or scale a ladder to reach products.
Dube said space is constrained whether the economy is growing or not. With strong consumer spending, there’s a need for more room to store that inventory. But when business is down, there may be a desire to consolidate into fewer warehouses.
3. Quality control and accuracy
Having software – and connecting its data to robotics – improves accuracy in goods storage and retrieval.
“There’s a digital aspect to the operation that’s just more consistent. When fewer hands touch the process, you make fewer errors,” Chesterfield said.
With a WMS, warehouse managers know where, within the warehouse, their SKUs are located in real time, Dube said.
Improved accuracy cuts down on mispicks, in which the wrong item is picked, packed and sent to the consumer. If a consumer ordered a red shirt but got a pink one by mistake, the consumer has to send it back, and the business has to pay for return shipping, re-inventory the item, and re-pick and re-ship the correct one. Dube said that one mispick typically costs around $100.
“If they can cut those mispicks in half, they can save hundreds, thousands of dollars a year,” Dube said.
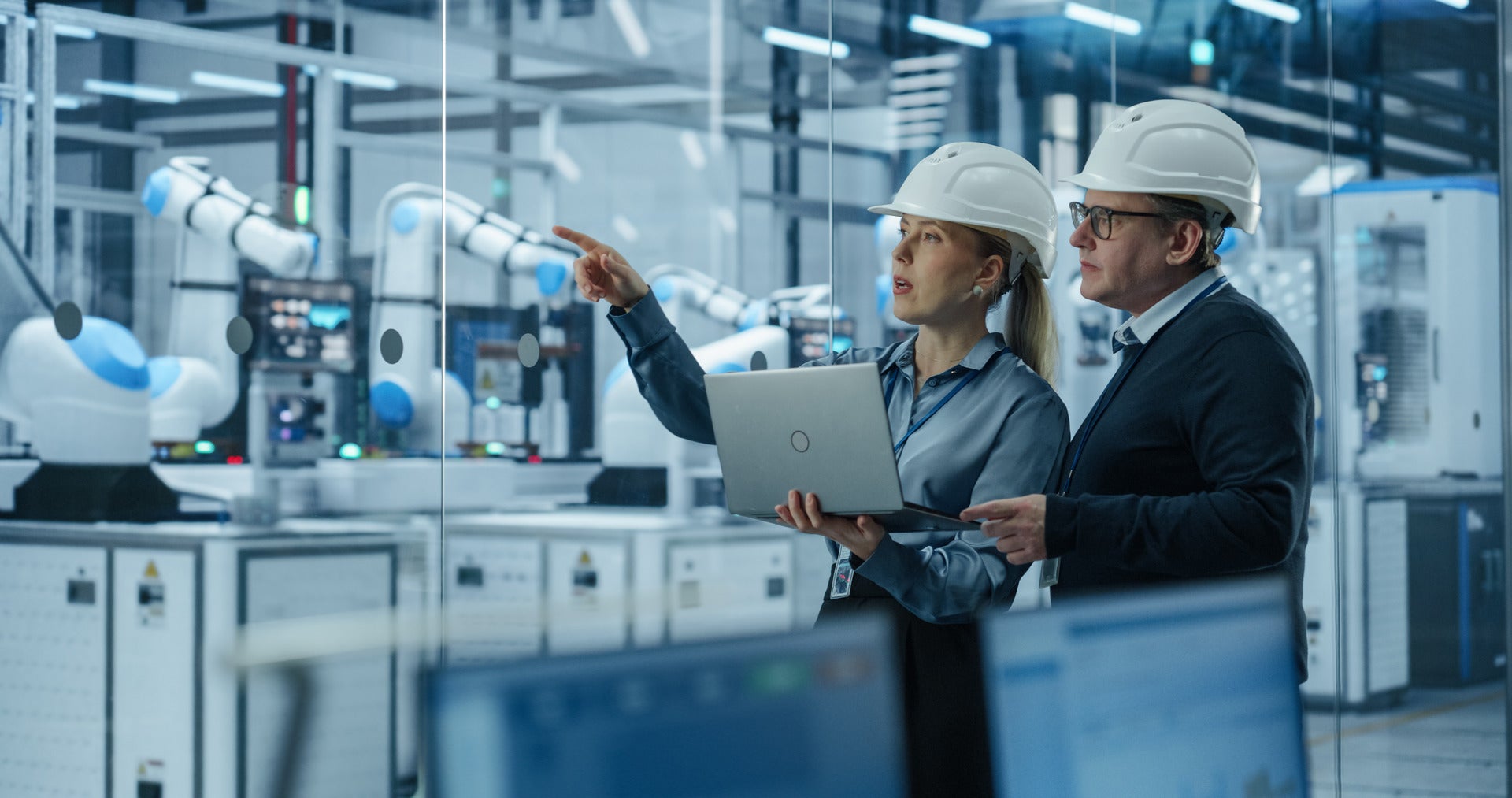
4. Faster operations
Small fixes can add up over time. SKU Distribution, a 3PL which provides warehousing and fulfillment services, uses cluster picking, which involves a warehouse worker collecting products for multiple orders at the same time.
Employees have a handheld device that guides them through the warehouse “in the most efficient manner,” said SKU Distribution Founder and CEO James Peacock. From one location, the worker then picks several products simultaneously, which eventually get sorted into 15 or 20 different orders.
“It saves us so much time,” Peacock said.
5. Flexibility to meet demand
During demand surges or peak holiday times, warehouse software and hardware allow warehouse operators to scale up quickly without trying to find staff available on short notice for temporary work.
“When volume spikes … you don’t have to panic or overextend your workforce,” – Ryan Chesterfield, founder of Auto-FC
During 2021’s peak season, DHL scaled up its use of picking robots by more than 30%, which helped it meet the uptick in demand, Rashid said.
One potential downside of relying on automation is the potential for technology or hardware failures, which could result in unexpected downtime as businesses wait for an expert to fix the software or for a replacement part to arrive.
Warehouse Automation Is Ramping Up
The rise of online shopping, paired with persistent labor shortages has put imence pressure on warehouses to streamline their operarational efficiency. As a result, automated robot systems are fast becoming a popular way to reduce dependence on manual labor.
Our own Moving Goods With Fewer Hands Report revealed that 15% of US logistic businesses recently adopted warehouse robotics, making them an even bigger growth area than autonomous vehicles. As more companies leverage the technology, failing to embrace automaton could make it harder for others to remain competetive and meet demands.
However, with most systems incurring high up-front costs, successful adoption hinges on investing in the right technology for your specific needs, as we explore next.
Making Smart Investments in Warehouse Automation
Warehouse automation is a big investment, which could pose a barrier especially to small businesses. There could be capital expenditures related to buying and installing automated machines, as well as repeat costs for software as a service or robotical rentals.
DHL, for one, has invested more than 1 billion Euros ($1.16 billion) into automation over the past three years. But the company takes a measured approach to its investments: “We will only implement automation solutions that have an acceptable ROI,” Rashid said.
Realizing the return on investment is key for supply chains. If the dollars poured into software and robotic arms result in fewer mispicks, lower worker turnover, the ability to scale for greater sales and enhanced brand reputation for customers, the investment may be worth it.
Kardex surveyed more than 100 of its customers about their ROI on automation. More than 78% saw ROI within a year, and nearly 59% saw it within six months.
For SKU Distribution, “we saw ROI instantly” once it implemented automation, Peacock said. The business was able to ship 3,000 to 4,000 per every one person, instead of per every six people.
CapEx decisions and ROI will vary based on each individual businesses’ operations, financial goals and priorities. Chesterfield said shippers need to understand their own costs and have internal benchmarks, so they can assess how vendors’ projections for ROI would actually play out for their company.
“If a solution doesn’t deliver a return within 12 to 24 months, it’s going to be hard to justify,” Chesterfield said.